Rigid-flex printed circuit boards (PCBs) combine the advantages of both rigid and flexible circuits. They offer design flexibility, durability, and reliability in various applications. Understanding the materials used in rigid-flex PCBs is crucial for engineers and manufacturers. This article explores the key materials that make up rigid-flex PCBs and their importance.
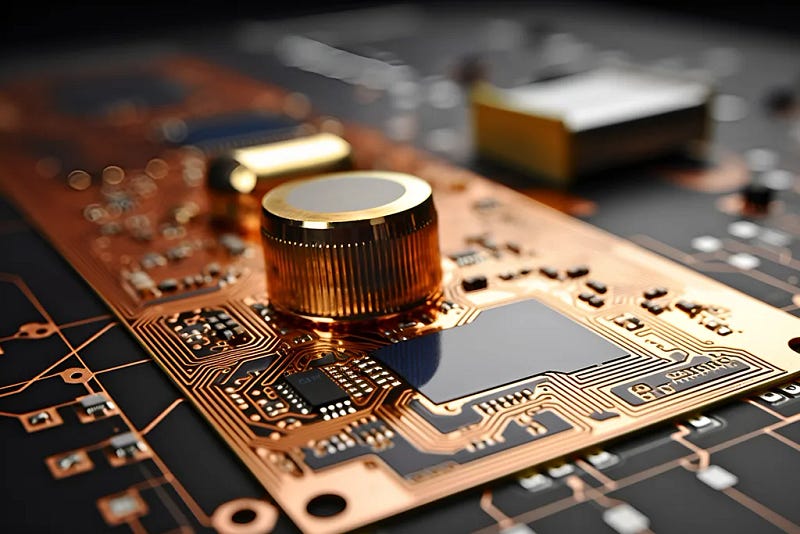
1. Substrate Materials
The substrate forms the backbone of any PCB, including rigid-flex types. In rigid-flex PCBs, manufacturers often use two main types of substrate materials: rigid substrates and flexible substrates.
- Rigid Substrates: Typically made from materials like FR-4, a composite of woven fiberglass and epoxy resin, rigid substrates provide mechanical strength. They support the components and ensure stability in the design. FR-4 is known for its excellent electrical insulation properties and thermal stability.
- Flexible Substrates: For the flexible portions, manufacturers commonly use polyimide or polyester. Polyimide is preferred for its high thermal resistance and flexibility. It can withstand bending and twisting without losing functionality. Polyester, while slightly less flexible, offers a cost-effective alternative for specific applications.
2. Copper Layers
Copper is a crucial material in rigid-flex PCBs. It serves as the conductive layer that allows electricity to flow between components. Manufacturers typically use copper foil, which they laminate onto the substrate during the PCB manufacturing process.
The thickness of the copper layer can vary depending on the application’s current-carrying requirements. Thicker copper layers provide better conductivity but can increase the board’s overall weight. Thin copper layers, on the other hand, save space and reduce weight, making them suitable for compact designs.
3. Adhesive Materials
Adhesive materials play a vital role in rigid-flex PCBs. They bond the rigid and flexible layers together, ensuring structural integrity. Manufacturers often use specialized adhesives that can withstand thermal cycling and mechanical stress.
Thermal stability is critical, especially in applications that experience temperature fluctuations. High-performance adhesives maintain their bonding strength under varying conditions. This characteristic is essential for the reliability of the final product.
4. Coverlay Materials
Coverlay materials protect the flexible areas of rigid-flex PCBs. They provide insulation and shielding against environmental factors like moisture and dust. Coverlay materials also enhance the PCB’s durability by adding a protective layer over the flexible substrate.
Manufacturers typically use polyimide or silicone-based coverlays for their excellent dielectric properties. These materials are both flexible and resistant to extreme temperatures, making them ideal for challenging environments.
5. Surface Finish
The surface finish of a rigid-flex PCB is critical for solderability and corrosion resistance. Manufacturers apply various surface finishes, including:
- HASL (Hot Air Solder Leveling): This traditional finish provides good solderability and is cost-effective. However, it may not be suitable for fine-pitch components.
- ENIG (Electroless Nickel Immersion Gold): ENIG offers excellent solderability and corrosion resistance. It provides a flat surface that is ideal for fine-pitch components and high-frequency applications.
- OSP (Organic Surface Protection): OSP is a more environmentally friendly option. It offers good solderability while maintaining a low profile.
Choosing the right surface finish depends on the application requirements and the components used.
6. Performance and Thermal Management Materials
In high-performance applications, thermal management is essential. Manufacturers may incorporate additional materials to enhance heat dissipation. These can include:
- Thermal Interface Materials (TIMs): TIMs improve thermal conductivity between heat-generating components and heat sinks. They help maintain optimal operating temperatures.
- Thermal Pads and Heat Sinks: These materials assist in dissipating heat from critical areas of the PCB, ensuring reliable operation.
Conclusion
In summary, rigid-flex PCBs utilize a variety of materials, each serving a specific purpose. Substrate materials, such as FR-4 and polyimide, provide structure and flexibility. Copper layers enable electrical conductivity, while adhesive materials ensure strong bonds. Coverlay materials protect the flexible areas, and surface finishes enhance solderability and durability. Additionally, performance materials support thermal management in high-performance applications. Understanding these materials helps manufacturers design reliable and efficient rigid-flex PCBs for diverse applications. As technology advances, the importance of these materials will continue to grow in the electronics industry.